在半导体制造业中,晶圆作为芯片的基础材料,其表面质量直接决定了最终产品的性能和可靠性。随着技术的不断进步,
晶圆表面缺陷检测系统已成为确保产品质量的关键环节。其中,切割槽的深度与宽度检测是评估晶圆加工精度和完整性的一项重要指标。
切割槽是在晶圆制造过程中,为了分离不同的芯片或进行后续工艺而刻蚀的微小沟槽。这些沟槽的尺寸精度对于芯片的封装、互联以及整体性能具有重要影响。传统的检测方法往往依赖于人工目视或使用简单的机械测量工具,这些方法不仅效率低下,而且容易受到人为因素的影响,导致测量结果的不准确。
为了克服这些挑战,晶圆表面缺陷检测系统引入了先进的图像处理和机器学习技术。通过高分辨率的光学显微镜或电子显微镜,系统能够捕捉到晶圆表面的微小细节,包括切割槽的形貌特征。随后,利用图像处理算法对捕捉到的图像进行预处理,如去噪、增强对比度等,以提高后续分析的准确性。
在图像预处理的基础上,系统采用特征提取技术来识别切割槽的边缘,并计算其深度和宽度。这一步骤通常依赖于边缘检测算法,如Canny算子、Sobel算子等,它们能够精确地定位切割槽的边缘位置。通过对边缘位置的进一步分析,系统可以计算出切割槽的深度和宽度值,并将这些值与预设的规格进行比较,以判断其是否符合要求。
此外,系统还结合了机器学习算法,通过对大量历史数据的训练和学习,系统能够自动识别和分类不同类型的切割槽缺陷,如过深、过宽、不规则形状等。这种智能化的检测方式不仅提高了检测的准确性和效率,还大大降低了人为因素对检测结果的影响。
最后为您展示一组晶圆表面缺陷检测系统图片,以便您更好地了解它!
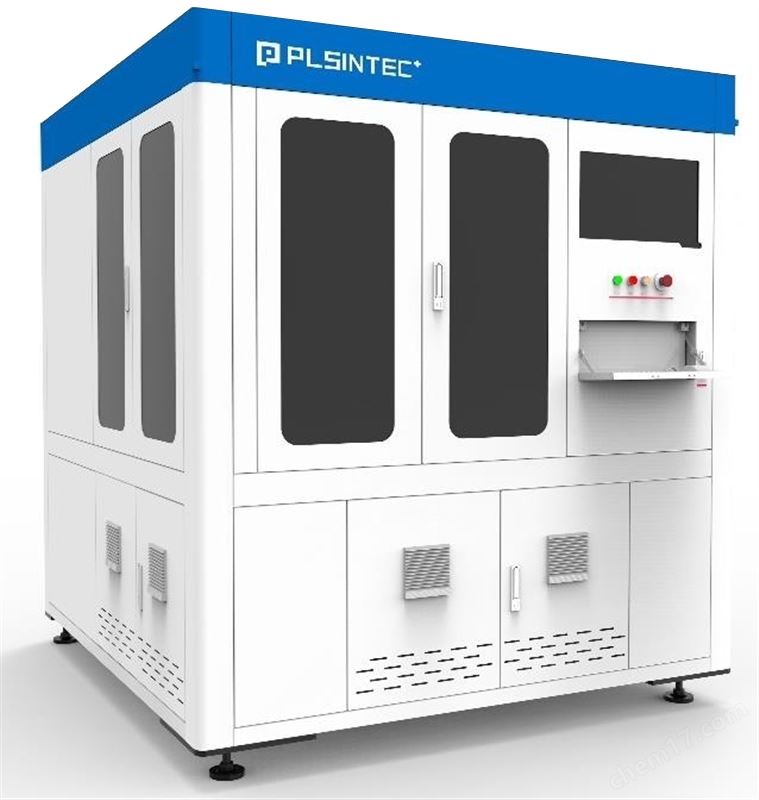
综上所述,晶圆表面缺陷检测系统中的切割槽深度与宽度检测技术对于确保半导体产品的质量和可靠性具有重要意义。随着技术的不断发展,这些检测技术将更加智能化、自动化,为半导体制造业的持续发展提供有力支持。同时,我们也期待未来能够出现更多创新性的检测技术,以应对日益复杂的晶圆加工需求和不断提高的产品质量标准。